Thermoplastic Polyurethane (TPU) filament is a popular choice among 3D printing enthusiasts and professionals due to its unique combination of flexibility, durability, and versatility. TPU is a type of thermoplastic that can be stretched and flexed without breaking, making it ideal for applications requiring elastic properties. This filament is commonly used for creating phone cases, wearable devices, flexible hinges, and flexible parts.
TPU’s popularity stems from its ability to produce objects that can endure mechanical stress and environmental exposure. It offers excellent resistance to abrasion, chemicals, and oils, which makes it suitable for both consumer and industrial applications. Moreover, TPU filament comes in various shore hardness levels, such as 77D > 70D > 55D > 95A > 85A > 83A > 80A > 75A > 70A allowing users to select the appropriate flexibility for their specific project needs.
Importance of Optimal Print Settings for TPU Filament
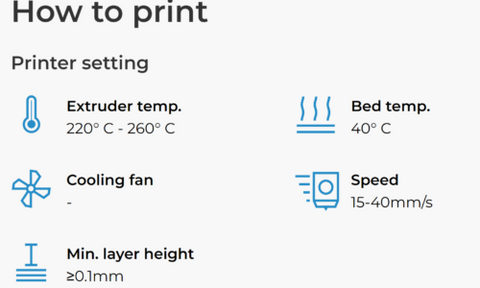
Printing with TPU filament requires precise control over print settings to achieve the best results. Unlike rigid filaments like PLA or ABS, TPU’s flexible nature can pose challenges if the settings are not appropriately calibrated. Optimal print settings ensure that the filament flows smoothly, adheres well to the print bed, and produces high-quality prints without issues like stringing, warping, or under-extrusion.
The key settings to focus on include print temperature, print speed, bed temperature, and retraction settings. Fine-tuning these parameters helps in minimizing common problems associated with TPU printing and ensures that the final print retains the desired properties of flexibility and strength.
Print Temperature
For TPU filament, print temperature plays a crucial role in ensuring proper extrusion and layer adhesion. A common range for TPU print temperature is between 220°C and 260°C. Setting the temperature too low can result in under-extrusion, leading to weak prints with poor layer bonding. Conversely, setting the temperature too high can cause overheating, resulting in stringing and blobs. An optimal temperature might be around 230°C, but this can vary based on the specific brand of TPU filament being used.
Print Speed
Due to TPU’s flexible nature, printing at high speeds can cause issues such as under-extrusion or filament buckling. Reducing the print speed helps maintain control over the filament flow and improves print quality. An optimal print speed for TPU is typically between 15-40 mm/s. Slower speeds allow the extruder to handle the filament more effectively, preventing issues like skipping or jamming.
Bed Temperature
Bed temperature is important for ensuring good adhesion of the first layer, which is critical for the success of the entire print. A heated bed set to around 40-60°C is generally recommended for TPU. If the bed temperature is too low, the filament may not stick properly, leading to warping or detachment during the print process. Using a temperature of around 50°C often provides a good balance for many TPU filaments.
Retraction Settings
Retraction settings need to be carefully adjusted to reduce stringing and oozing, which are common issues with TPU. Since TPU is more elastic, it requires lower retraction distances and speeds compared to rigid filaments. For instance, a retraction distance of 1-2 mm and a retraction speed of 20-30 mm/s are typically effective. These settings help in pulling back the filament just enough to prevent stringing without causing jams or under-extrusion.
By adhering to these optimized settings, users can significantly enhance the quality of their TPU prints. Proper print temperature ensures smooth extrusion and strong layer adhesion, while a moderate print speed helps maintain control over the filament. The correct bed temperature aids in good initial layer adhesion, and fine-tuned retraction settings minimize stringing and oozing. These adjustments collectively lead to superior prints that showcase TPU’s flexibility and durability.
Additional Tips
Filament Handling
Proper storage and handling of TPU filament are crucial as it is hygroscopic and can absorb moisture from the air. Keeping it in a dry box or using desiccants can prevent moisture-related print defects.
Use Direct Drive Extruders
For printing with TPU filament, only direct drive extruders should be used. Direct drive extruders provide better control over filament feeding, which is crucial for handling TPU's flexible nature. The reduced distance between the extruder and the nozzle minimizes filament buckling and improves print quality. Additionally, TPU filament cannot be fed through an Automatic Material Switching (AMS) machine, as its flexibility can cause feeding issues and jams. Using a direct drive extruder ensures smooth and consistent extrusion, leading to higher quality prints.
Optimize Slicer Settings
Customizing slicer settings for TPU can significantly impact print quality. Adjust layer height, wall thickness, and infill density to suit the flexibility requirements of the print. For instance, thicker walls and higher infill can enhance the structural integrity of flexible parts.
Maintain a Clean Nozzle
Keeping the nozzle clean and free of debris ensures smooth filament flow. Regular maintenance and occasional cold pulls can prevent clogs and ensure consistent extrusion.
Troubleshooting Common Issues with TPU Filament Printing
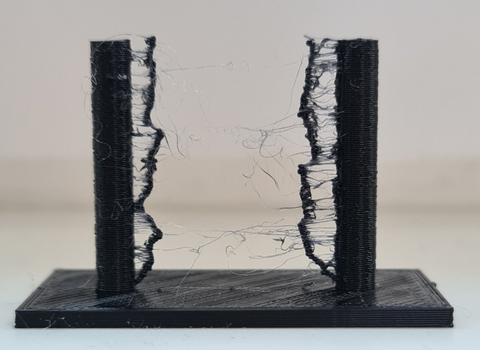
Stringing
Stringing occurs when thin strands of filament are left behind during non-print moves. To mitigate this, adjust retraction settings, reduce print temperature, and increase travel speed.
Warping
Warping is less common with TPU due to its flexibility, but it can still occur. Ensure proper bed adhesion by using a heated bed and adhesion aids. Also, print in an enclosed chamber to maintain a stable temperature.
Under-extrusion
Under-extrusion can result from incorrect print temperature, clogged nozzles, or filament feeding issues. Check the filament path for obstructions, ensure the nozzle is clean, and verify that the print temperature is within the recommended range.
Layer Shifting
Layer shifting can be caused by mechanical issues or improper calibration. Ensure that the printer’s belts and pulleys are tight and that the print bed is level.
Innovations in TPU Filament Technology
The development of TPU filament continues to evolve, with manufacturers introducing new formulations to enhance its properties. Innovations include TPU blends that offer improved strength, greater flexibility, and enhanced printability. Additionally, some TPU filaments are now designed to be more resistant to UV light and harsh chemicals, expanding their range of applications.
Advanced TPU filaments with embedded conductive materials are also being developed, opening up possibilities for creating flexible electronic components. These advancements are pushing the boundaries of what can be achieved with TPU in both consumer and industrial 3D printing.
Mastering TPU Filament Printing for Superior Results
Mastering TPU filament printing requires understanding its unique properties and optimizing print settings to address its challenges. By carefully adjusting print temperature, speed, bed temperature, and retraction settings, you can achieve high-quality prints with the desired flexibility and durability.
Employing tips and techniques such as using direct drive extruders, maintaining a clean nozzle, and calibrating your printer regularly will further enhance your printing experience. Staying updated with the latest innovations in TPU filament technology can also provide new opportunities for your 3D printing projects.
With practice and attention to detail, you can leverage the full potential of TPU filament to create flexible, durable, and versatile prints that meet a wide range of applications.