The use of 3D printing technology has revolutionized the manufacturing industry, allowing for faster prototyping and more customized production.
Setting up a 3D printing farm can further maximize efficiency and output, especially when using high-quality materials like SUNLU PLA filaments. In this ultimate guide, we will delve into the best practices for running a successful 3D printing farm, including tips on equipment maintenance, workflow optimization, and quality control.
Streamlining your processes for maximum efficiency
To achieve peak efficiency in your 3D printing farm, it is crucial to streamline your processes. Implementing a systematic workflow, scheduling regular maintenance checks, and optimizing print settings are key factors in maximizing output.
Utilize software tools to automate repetitive tasks and monitor production progress in real-time. Additionally, establishing quality control measures and conducting regular calibration tests will ensure consistent and precise prints. By fine-tuning your processes and embracing continuous improvement, you can enhance productivity and elevate the overall performance of your 3D printing farm.
Investing in the right equipment and software
Selecting the appropriate 3D printers and software is paramount in enhancing the efficiency of your printing farm. Consider the size and capabilities of the printers to match your production needs. Opt for reliable and durable equipment to minimize downtime and maintenance costs. Invest in advanced slicing software to optimize print speed and quality.
Printers: Power, Speed, and Reliability
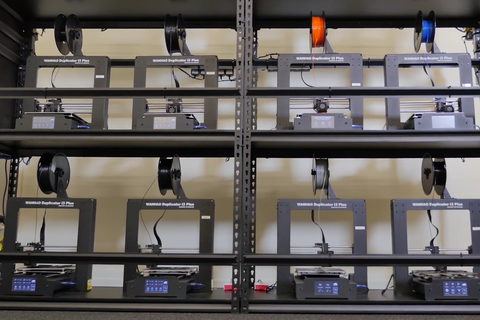
Identify your production needs: Consider factors like print volume, material compatibility, and desired part size.
Prioritize reliability and durability: Minimize downtime and maintenance costs with robust printers. Look for established brands known for quality and support. For instance, the Bambu Lab range of 3D printers is renowned for its speed and accuracy, making it ideal for high-volume production.
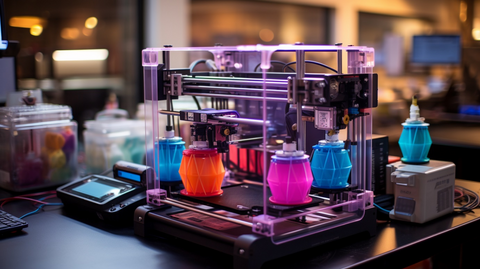
Explore advanced features: Features like multi-material printing, automated bed leveling, and enclosed build chambers can significantly enhance efficiency.
Implementing a comprehensive maintenance schedule
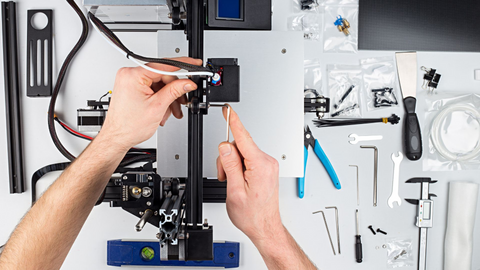
Just like a well-oiled machine, a 3D printing farm thrives on preventative maintenance. Here's why a proactive approach is essential for keeping your printers running smoothly and your production on track:
Regular inspections and cleaning can identify minor issues before they snowball into major malfunctions.
Extending the Lifespan of Your Printers: 3D printers, like any machine, have a finite lifespan. By regularly cleaning and lubricating components, you minimize wear and tear, extending the overall life of your investment. Imagine getting an extra year or two out of your high-end Bambu Lab printer – that's significant savings in the long run!
Maintaining Optimal Performance: Over time, 3D printers can fall out of calibration, leading to inconsistent print quality and potential defects. Routine calibrations ensure your printers are operating at peak precision, delivering consistent, high-quality results for every project. This also includes regularly updating the firmware of your machines.
Schedule is Key
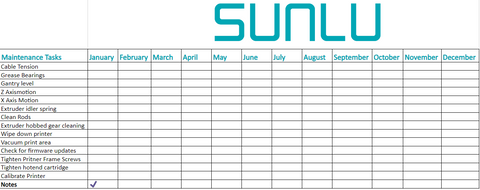
Develop a regular maintenance schedule tailored to the specific needs of your printers and the materials you use. weekly or monthly cleaning, regular inspections, and monthly calibrations might be a good starting point.
You can utilize Our 3D Printer maintenance sheet to keep track of the tasks carried out !
Detailed Records: Maintain a log of maintenance performed, including the date, any issues identified, and the actions taken. This record-keeping helps identify recurring problems and allows you to adjust your maintenance schedule accordingly.
Addressing Issues Promptly: Don't ignore minor glitches or imperfections in your prints. Prompt attention to these issues can prevent them from escalating into bigger problems down the line.
By implementing a proactive maintenance plan, you'll transform your 3D printing farm from a reactive operation to a well-oiled machine of efficiency, ensuring consistent performance, high-quality output, and a maximized return on your investment.
Utilizing batch processing and automation
Imagine you have 100 identical figurines to print. Traditionally, you'd print them one by one, leading to significant idle time between prints. Batch processing groups similar print jobs together, allowing you to print them simultaneously on multiple printers. This dramatically reduces overall production time.
The Magic of Automatic Ejection and Restart
Here's where things get exciting: many farms leverage automatic ejection and print start to further optimize batch processing, especially for repetitive tasks.
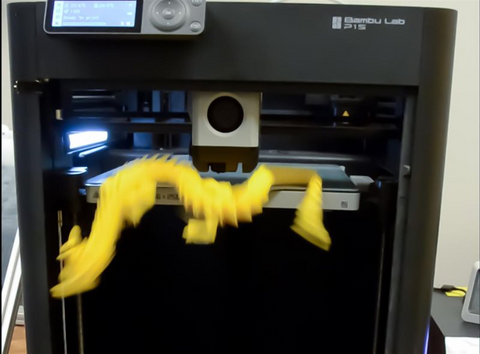
Imagine this scenario, You need to print those 100 figurines. With automation, you can designate a specific group of printers within your farm for this job. Once a print finishes, a custom G-code script (we'll discuss this script in detail later) activates, automatically ejecting the completed figurines from the print bed. The script then initiates a new print cycle on the same machine, repeating this process until all 100 figurines are complete.
Benefits Galore:
Reduced Labor Costs: Automatic processes minimize the need for manual intervention, freeing up your staff for other tasks.
Faster Production Times: Batch processing and automation significantly accelerate production compared to traditional, single-run printing.
Consistency and Scalability: Automated processes ensure consistent quality and allow you to easily scale production up or down based on demand.
Unveiling the G-code Secret:
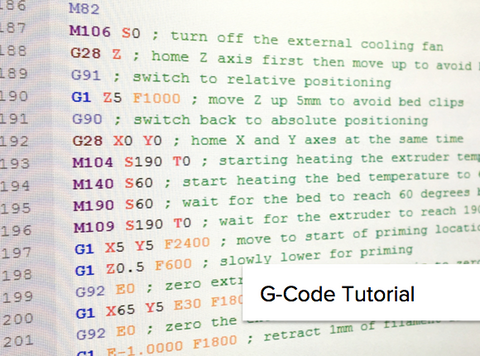
We mentioned a custom G-code script for automatic ejection and restart. G-code is the language that instructs 3D printers. By modifying this script (a process we'll explore in future sections), you can program specific actions, like raising the print bed, cooling it down, and using the print head itself to gently push the finished parts off the bed. This eliminates the need for manual removal, streamlining the entire process.
This is the end of my machine end g-code.
G90 ; absolute positioning
G1 X128 Y250 F3600 ; park
; ======== eject parts
G0 X128 Y256 ; move to middle back of bed
G0 Z1 ; raise bed until nozzle is almost touching
M106 P2 S255 ; turn on aux fan to cool bed quickly
M190 30 ; wait for bed to be cold
;G04 S300 ; give the part time to break free so pushing it is easier
M106 P2 S0 ; turn off aux cooling fan
G0 Y0 F1000 ; push part of bed
; ==== end eject
M220 S100 ; Reset feedrate magnitude
M201.2 K1.0 ; Reset acc magnitude
M73.2 R1.0 ;Reset left time magnitude
M1002 set_gcode_claim_speed_level : 0
M17 X0.8 Y0.8 Z0.5 ; lower motor current to 45% power
Efficiency is the cornerstone of a successful 3D printing farm. By embracing technology advancements, staying informed about industry trends, and fostering innovation within your team, you can streamline processes and maximize productivity. Batch processing and automation techniques, can transform your 3D printing farm into a highly efficient production powerhouse.
Continuous improvement and a culture of innovation will help you stay competitive and ensure long-term success in the ever-evolving world of 3D printing. Keep implementing new strategies, gathering feedback, and refining your workflows to achieve optimal efficiency and stay ahead of the curve.